Blending Craft and Technology: A Hands-On Approach to Design and Fabrication
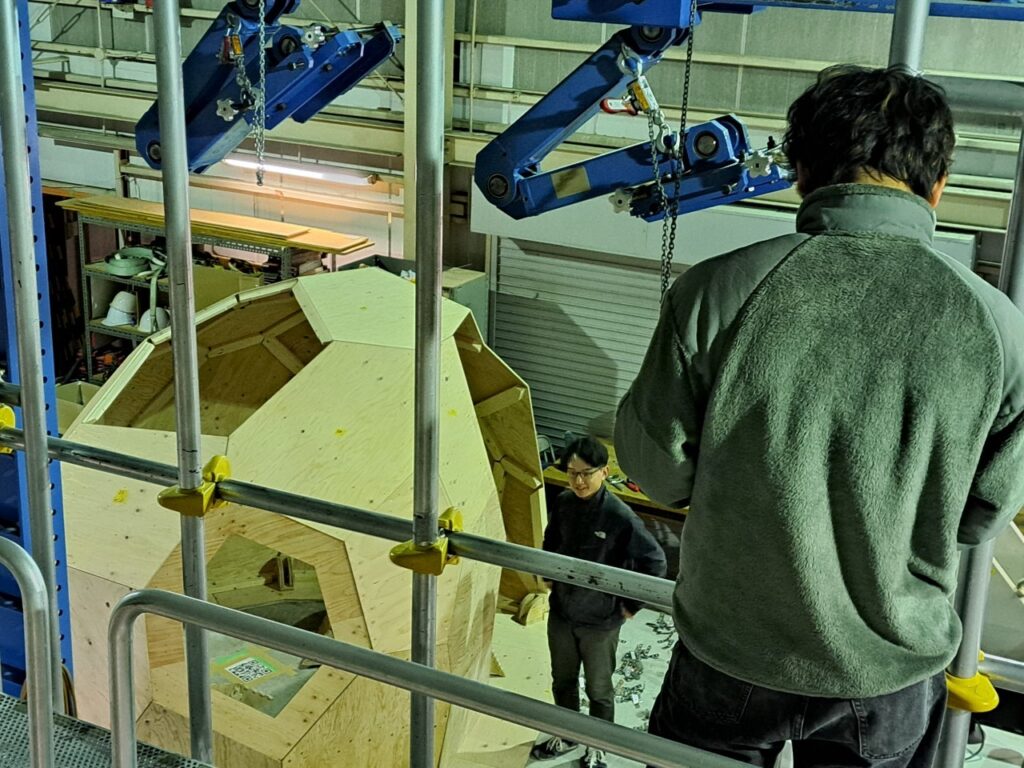
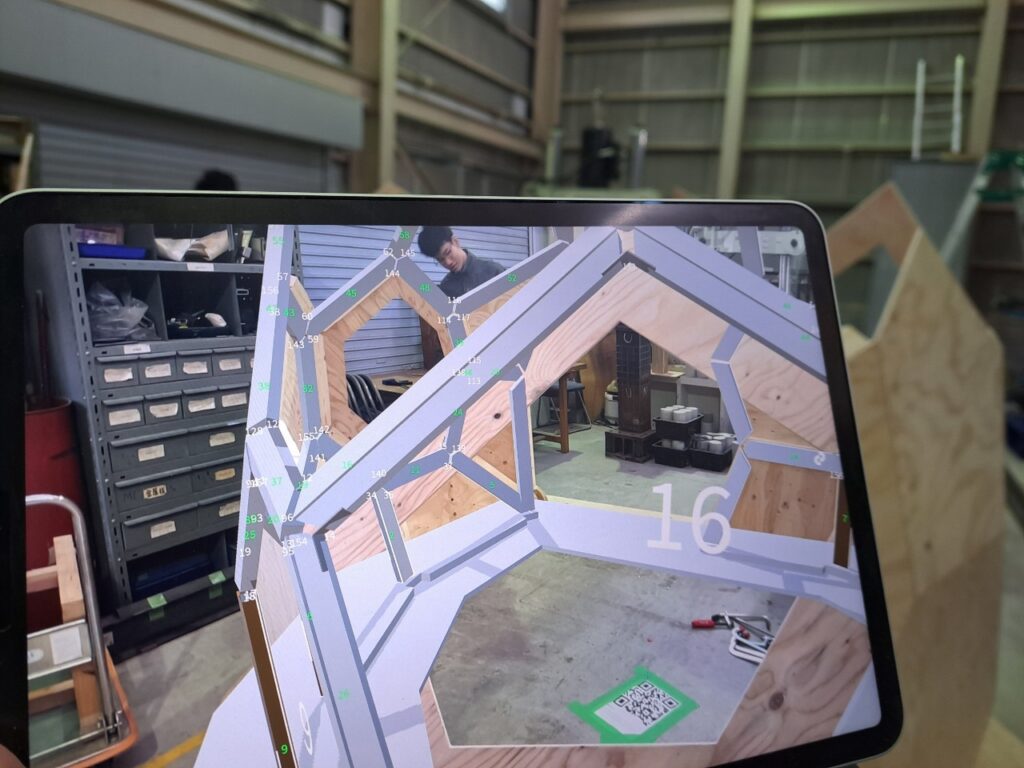
March 21 – Kinetic Stool Pavilion
The students at Toyota Kosen pushed forward with the design-build process. After I provided them with a few additional pointers, they successfully constructed the pavilion inside one of their school buildings. The temporary site was spacious enough to accommodate the structure while giving them ample room to work around it.
As part of the project, the students implemented innovative building strategies, such as integrating VR with QR codes to manage components. This allowed them to use software guidance to determine the exact placement of each piece.
The mock-up build was a success, with all components fitting together as intended. I advised them to avoid fully securing all joints, instead only fastening the necessary connections. I was concerned that repeatedly screwing and unscrewing parts could loosen the holes, potentially compromising the structure’s stability.
Another important discussion focused on reinforcing the foundation with M8 bolts. Initial tests suggested the structure might not require them, but as a precaution, I recommended adding at least three bolts per member to ensure structural integrity.
The second iteration of the entrance design became the final version. Due to time constraints, the students were unable to explore additional refinements to further enhance the pavilion’s design quality.
Bulgaria Pavilion Sign for Expo 2025 Osaka
I was unable to participate in the hands-on construction of the mock-up build due to another project. I was commissioned to produce a sign for the Bulgaria Pavilion, which will be featured at Expo 2025 Osaka, presented by the World Expo.
The design document was provided by KMDW (Kobayashi Maki Design Workshop), the design team behind the Bulgarian Pavilion. The sign reads Болгария in Russian, meaning “Bulgaria.”
The sign consists of eight panels, one for each letter, with each panel measuring 800 × 1600 mm. The panels will be CNC-machined from black poly-lumber, a material that has a poly-coated front and back face with a softwood core.
While the overall design was straightforward, the intricate details of certain letters presented a challenge when generating the cutting data. I was using a 3mm Amana Tool 48302-K CNC Spektra compression bit, but some of the letters contained details smaller than 3mm. While there were workarounds, they would have significantly increased processing time for each board.
Given the tight schedule, I asked the designers to revise their design so that we could keep the CNC processing time to approximately three hours per board or less.
また、デザインの担当がFarrasからMasaへ引き継がれました。これまで進めていた樹木の配置解析を基にした通路のデザインから、2〜3人が入れるドーム型構造へと方向性を変更しました。このドームのサイズは約2.5m×2.5mで、プロジェクトの時間的・予算的な制約を考慮して決定しました。
その他の進行中のプロジェクト スケートボードランプ – ほぼ完成
スケートボードランプのプロジェクトも完成間近ですが、Fusion360でのGコード処理に問題が発生しました。設計図の穴が誤って**ブレップ(BRep)**として認識され、手作業での修正が必要になりました。手間はかかりましたが、プロジェクトは順調に進んでいます。
DIYコートハンガー – 誰でも作れるカスタマイズ可能なデザイン
最近、お客様からコートハンガーのオーダーをいただきました。これを機に、誰でも簡単に作れるDIYシステムを設計しようと考えています。合板や30×30mmの木材などの入手しやすい材料を使用し、3DプリントやCNC加工で製作できるジョイントパーツを提供する予定です。
さらに、Webサイト上でサイズをカスタマイズできる機能を開発し、高さや幅を自由に調整できるようにします。これにより、ユーザーが選んだ寸法に合わせて3Dプリントジョイントの角度も自動調整される仕組みになります。
今後の展望 これらのプロジェクトを通じて、デジタルファブリケーション、機能性、美しさのバランスをさらに追求していきます。今後もパビリオンの試作、DIYデザイン、新たなオリジナル家具プロジェクトの進捗を更新していきますので、お楽しみに!